Common Mistakes in Engine Rebuilding and How to Avoid Them
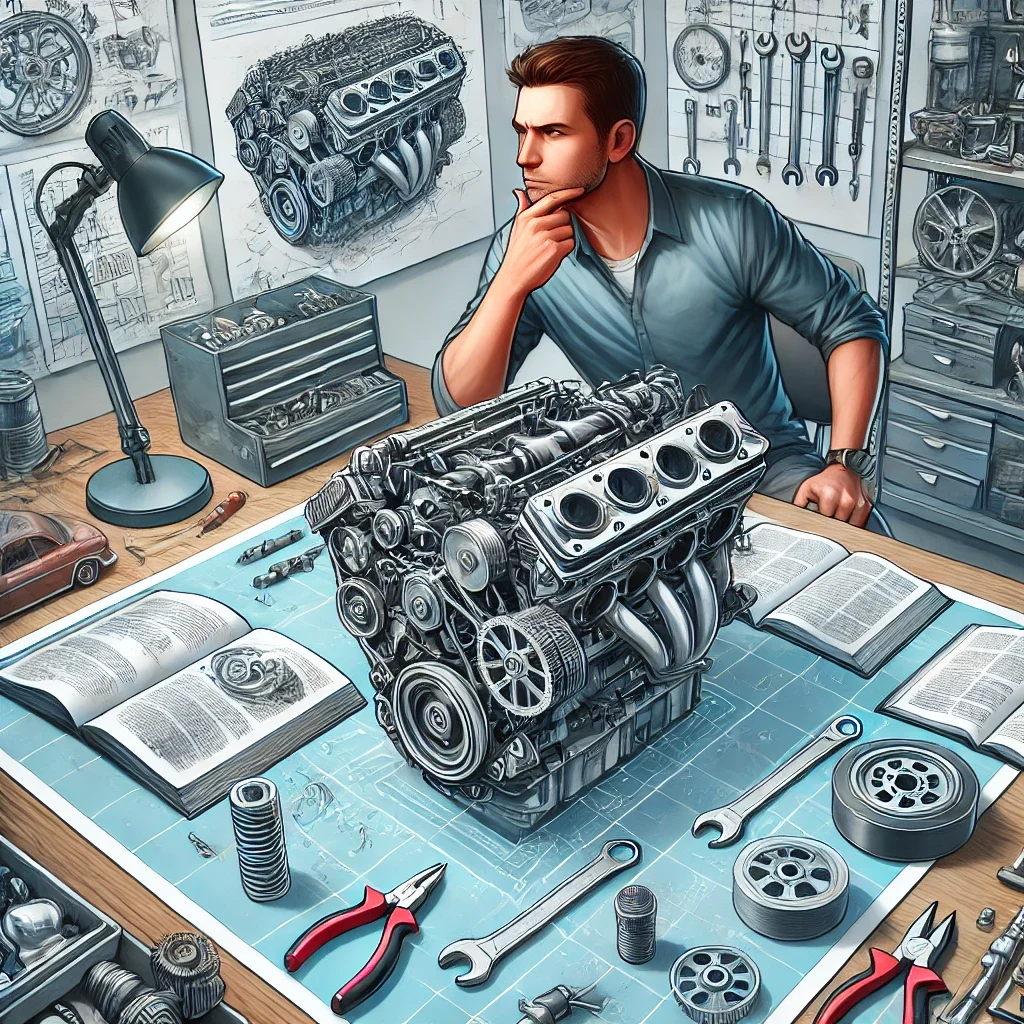
Rebuilding an engine can seem like a daunting task, especially for those new to mechanics. Yet, with the right information and diligence, it’s a rewarding endeavor that can lead to better engine performance and longevity. However, mistakes during the rebuilding process can lead to disaster and additional costs. Here, we’ll explore some common mistakes encountered in engine rebuilding and provide tips to avoid them.
1. Inadequate Cleaning of Components
One of the most critical steps in engine rebuilding is ensuring that every component is meticulously cleaned. Neglecting this can lead to contamination and poor performance. Dirt and grime can affect the engine’s lubrication and cooling systems.
How to Avoid It: Take the time to clean each component thoroughly before reassembly. Use appropriate solvents and tools to ensure that your engine block and parts are spotless. Remember, a clean engine is essential for reliable performance.
2. Failure to Inspect Components Properly
Often, builders may rush through the inspection process or fail to carry out a thorough check on critical components such as gaskets, bearings, and cylinder heads. Overlooking warpage or wear can lead to severe issues once the engine is operational.
How to Avoid It: After cleaning, inspect each part carefully for any signs of damage or wear. Pay attention to gasket surfaces, looking for any rust or discoloration, which may indicate leaks. Conduct pressure tests and compression checks when needed.
3. Using Incorrect Tools or Fasteners
Using the wrong tools or hardware during the rebuild can lead to improper assembly and damage. For instance, using mismatched bolts can compromise the integrity of components.
How to Avoid It: Invest in proper tools designed for engine rebuilding. Refer to your engine’s specifications and service manual for the correct fasteners and torque settings. Always double-check your tools and parts before starting the assembly.
4. Failing to Follow Torque Specifications
Improper torqueing of bolts can lead to catastrophic failures, including warped heads or blown gaskets. Many novice rebuilders tend to either under-torque or over-torque fasteners.
How to Avoid It: Follow the torque specifications outlined in your engine’s service manual precisely. Use a calibrated torque wrench and follow the recommended tightening sequence to ensure uniform pressure across components.
5. Skipping the Break-In Process
After rebuilding, engines require a break-in period to ensure that the components settle properly. Skipping or rushing this step can lead to premature wear and reduced engine performance.
How to Avoid It: Follow a structured break-in process, which usually includes varying your speed and load during the initial drive cycles. This helps to properly seat the piston rings and allows all components to find their optimal interaction.
Conclusion
Rebuilding an engine can be a fulfilling project, but attention to detail is paramount. By avoiding these common mistakes, you can ensure a smoother rebuilding process and a more reliable engine. Don’t let misinformation hinder your progress; refer to comprehensive guides and seek advice from experienced builders whenever necessary. With diligence and patience, you’ll not only bring your engine back to life but also enhance its performance for years to come. Happy rebuilding!